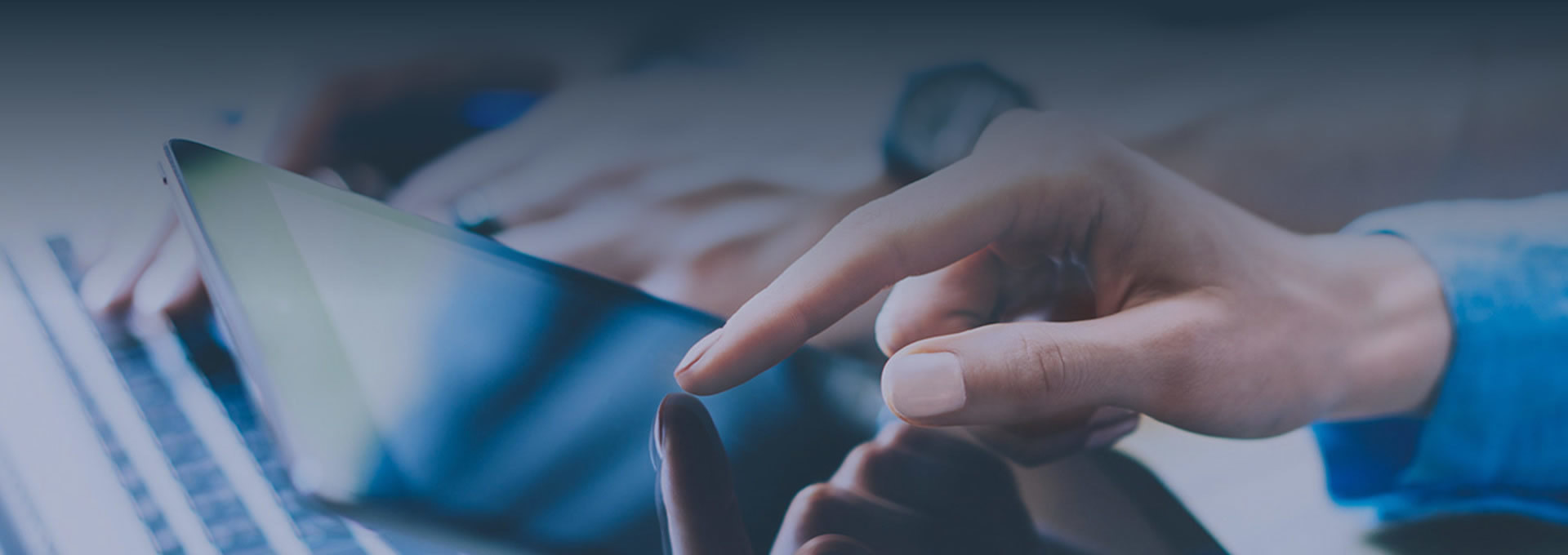
NEWS
08
2023
-
12
Medical Vials: A Crucial Element in Modern Healthcare
Abstract:
In the current healthcare market every aspect is crucial as medical vials play a critical function. These seemingly common bottles hold the promise of health for humans and play a vital role in the functioning in the health system. This paper will examine the significance to medical vials, as well as their multiple functions in the current healthcare environment and will take readers through the world of microscopic health and understanding the technological and innovative aspects that lie behind it. By reading this paper readers will gain an knowledge of the beauty of this medical device as well as the enormous responsibility it bears.
Introduction:
In the modern field of medicine, every aspect is important. Medical vials, crucial for the storage and administration of medication, play an important part for the medical system. These simple bottles are made to ensure the effectiveness, stability and security of medicines.
Historische Evolution of Medical Vials:
Medical vials are a part of a long-running tradition which dates back to prehistoric times. The first glass vials have been discovered throughout Egypt and Rome and were made by hand. The vials were generally green and came in different designs. As time passed glass vials began to be utilized more frequently in the medical field specifically in Europe. Glass vials were used by doctors to store and distribute medications such as powders, liquids and solids. The manufacturing and design of glass vials has also advanced as time passed, and became more sophisticated and precise.
In the present, advancements in glassmaking technology have resulted in significant advancements in the manufacturing of medical vials. Production lines that are large-scale and technological advances have made it possible to manufacture glass vials in a more efficient manner and in more intricate design and shapes.
materials for the medical Vials:
Medical vials are vital containers for storage and transport in the field of healthcare that are primarily used for storage and transferring medication. The majority of these vials are made from special glass that include borosilicate glass, with low-borosilicate glass being most popular. This section explains the distinct characteristics and benefits of both glass materials.
Borosilicate glass:
- High chemical stability.
- Protects its original characteristics of medicine.
- Resists high temperatures and sterilization processes with ease.
- It has high heat resistance and mechanical toughness, leading to the long-lasting service duration.
- Perfect for the production of long-term storage vials for medication.
But, it's important to keep in mind that although it has numerous advantages, it has the cost of production and manufacturing difficulties. The excellent chemical stability could cause the creation of an inert layer on the glass's surface, which could affect the interactions between the drug with the vial of glass. Thus, the selection of the borosilicate glass should be based on the cost, the manufacturing intricacies and ensuring that it does not affect the effectiveness and quality of the drug.
Low-Borosilicate Glass:
- Presents a more cost-effective alternative.
- Exhibits high heat resistance and mechanical strength.
- Suitable for crafting short-term storage medication vials, such as antibiotic injections.
- Features lower chemical stability and temperature stability.
While low-borosilicate glass offers cost advantages and meets basic requirements for medication storage, its lower chemical and temperature stability must be considered. Depending on the application, careful evaluation is needed to ensure it aligns with the specific needs of the medications it will store.
Production Process for Medical Vials:
The manufacturing process for medical vials comprises several key steps:
Melting:
- The process involves melting glass raw ingredients at high temperatures to make a uniform glass.
- It is a furnace which requires the precise control of temperature as well as raw mixing ratios.
- The glass raw ingredients are mixed, melted and clarified to create an even liquid glass that has no stones or bubbles.
Blowing:
- Uses a blowpipe to form the glass liquid into an elongated vial.
- It involves pouring out liquid glass, then cooling and solidifying it, later making it into the desired shape by blowpipe.
- Needs precise control of temperature as well as blowing pressure to meet the specified specifications for shape and size.
Shaping:
- It involves further processing of blow vials to get them into their final size and shape.
- This includes cutting, grinding and polishing to create a smooth, uniform surface and form.
- A strict control of the quality and precision of processing in order to meet the requirements.
Annealing:
- This involves subjecting the molds to high-temperature treatments to reduce internal stress and lessen brittleness.
- The process involves holding the vials at extreme temperatures during a predetermined time, which allows internal structure adjustments for less the brittleness of the material and better durability to impacts.
- It requires the precise control of temperature as well as time in order to maximize the properties of vials.
Finishing:
- The final step which includes processing the mouth of the bottle grinding, cleaning, and cleaning.
- It includes cutting, grinding and cleaning the bottle's mouth to create a smooth, regular surface.
- It is essential to have a strict control of the bottle's mouth size as well as its quality of the surface to ensure the sealing is reliable and secure.
Controlling quality and adhering to requirements in the production process are crucial for ensuring security and safety of medical vials.
Form and Design of Medical Vials:
Medical vials are made in a variety of designs and shapes to meet the storage and usage requirements of various medicines. Common shapes and styles include:
Straight-Neck Vials:
- The neck is upright for simple refilling as well as dispensing.
- Avoid splashing or waste while moving, increasing efficiency.
- The product has excellent sealing properties to ensure stability and efficacy of medication.
Wide-Mouth Vials:
- Have a longer neck to allow to make it easier to add large or viscous medicines.
- Improve your comfort by preventing neck congestion during medication administration.
- You must use a sealer that is effective to ensure the quality of your medication.
Sealed Vials
- Utilize gaskets and caps with special features to ensure the seal of medication when it is stored and transported.
- Stop medications from being impacted by moisture, air and pollution.
- Might require skill and strength to close and open and closing the door, which may be uncomfortable for some users.
Dropper Vials:
- Include a dropper integrated to ensure accurate medication dispensing.
- Increase the accuracy and security of medications while using.
- Regularly clean-up and disinfection is essential to ensure that there is no cross-contamination.
The Common Issues and Solution Medical Vials:
Medical vials can experience frequent problems while in use which include cracks, breaks, and inadequate sealing. Quick solutions and preventive measures are required to ensure safety storage and usage of medication.
Cracks:
- Causes: Friction, impact High or even low temperature.
- Solutions: Avoid contact and friction, as well as ensuring a stable temperatures in the storage area.
Breakage:
- Causes: Impact of external force or inadvertent use.
- Solutions: Avoid impact that is too strong Use appropriate devices and tools.
Poor Sealing:
- The cause is damage to the gasket or cap of bottle.
- Solutions Solution: Regular examination and replacing of the bottle gasket and cap. Keep medications dry and clean when it is stored and used.
To make sure that medication is safe pay attention to:
- Assuring that the supplier from which you purchase medical vials is reliable and is in compliance with relevant standards and regulations.
- Monitoring medical vials for cracks, cracks, or defects prior to use to ensure a good seal performance.
- Follow the medication's instructions for use and storage requirements to protect medications from getting influenced by moisture, light and high temperatures.
- Avoiding friction and excessive impact on medical vials during use to keep the medication safe and ensure efficiency.
- The medication should be stored in an air-tight and dry environment after use, accompanied by frequent inspection and maintenance of cap caps and gaskets.
How to choose a suitable Pharmaceutical Packaging Company: Xinde Pharmaceutical Packaging's experience and Tips
Selecting the best pharmaceutical packaging provider is essential to ensure the security, efficacy and compliance with the use of drugs. Here are a few suggestions to assist you in choosing the most appropriate supplier:
Find your requirements and standards:
- Define your packaging requirements clearly Include the type, the material size, dimensions, and the printing specifications.
- Limit your search by identifying companies that satisfy your specific needs.
Know the Supplier's Qualifications and Certificates:
- Check if the vendor is certified and has the relevant qualifications.
- Certifications like ISO 11607, ISO 9001 and FDA will attest to the highest quality standards and rigorous controls on quality.
Evaluate the Supplier's Strength and experience:
- Assess the capacity of the supplier's production as well as customer base and reputation in the industry.
- Learn about the experience of the supplier and the variety of clients served as well as the packaging solutions offered.
Prioritize Support and Service:
- Make sure the vendor offers complete support and services, including manufacturing, design, prototyping logistics, and design.
- Choose a provider that can provide custom solutions that are tailored to your particular requirements.
See Feedback and Suggestions
- Get feedback from your friends or partners as well as associations of industry.
- Be aware of the experiences of other customers of the company to assess its their reputation and quality of service.
To conclude, selecting the right pharmaceutical packaging company requires a thorough examination of qualifications, certifications and the strength of their experience, as well as support for service. With over two decades of expertise and pertinent accreditations Xinde Pharmaceutical Packaging is equipped to offer high-quality products for pharmaceutical packaging. For more information, get in touch with us.
Previous page
More News

Customer message