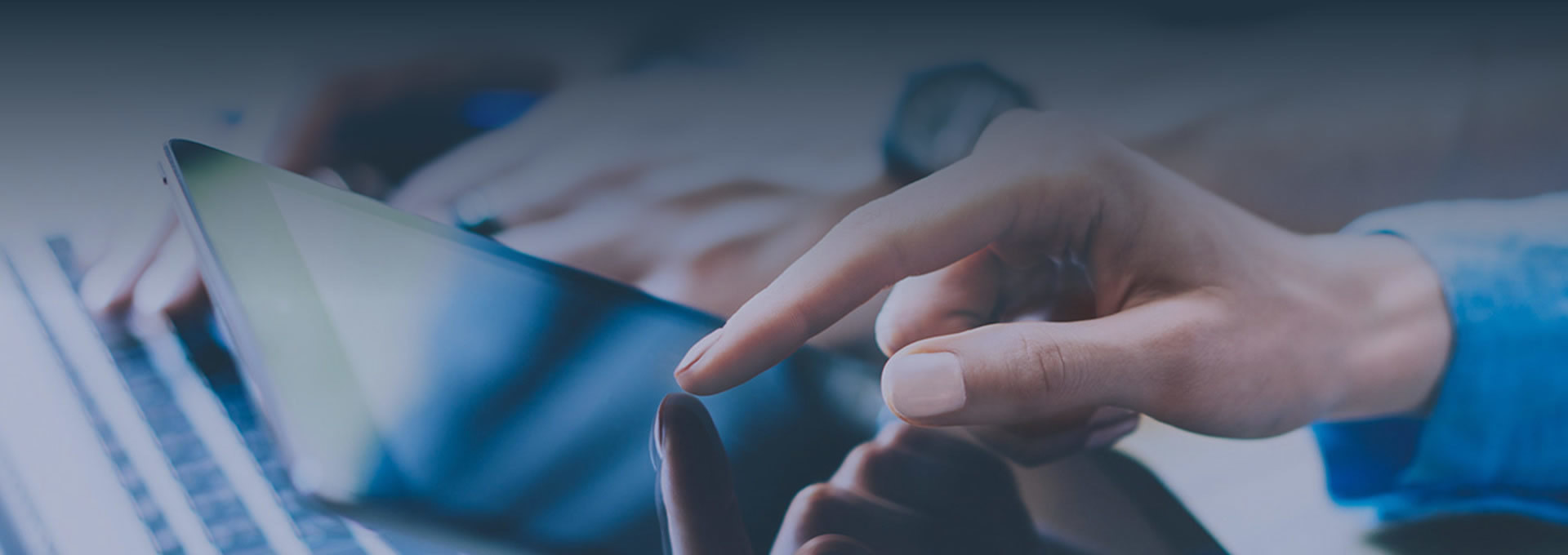
NEWS
23
2024
-
02
Glass Ampoules - The Preferred Choice for Pharmaceutical Packaging
Glass ampoules have been used for decades to store pharmaceuticals, due to their inertness, strength, and ability to be sterilized. As the pharmaceutical industry continues to grow, the demand for high-quality glass ampoules is higher than ever. Choosing the right glass ampoule manufacturer is critical for producing consistent, reliable products.
What are Glass Ampoules?
Glass ampoules are small, sealed glass containers used to store liquid pharmaceuticals, reagents, and chemicals. The glass tube is sealed at both ends after filling to protect the contents from oxygen and contamination. Ampoules are designed for a single use - once opened, the contents cannot be resealed.
The most common sizes range from 1mL to 20mL, though ampoules over 50mL can be produced. Translucent amber glass filters out UV light to protect light-sensitive contents. The long, thin design allows the entire solution to be dispensed accurately.
Benefits of Glass Ampoules
Glass has many advantages that have kept it the top choice for pharmaceutical packaging for over a century:
Inertness - Unlike plastics, glass does not react with or leach chemicals into the contents. This prevents contamination or degradation.
Temperature resistance - Glass ampoules can be autoclaved for sterilization and resist freezing or heating during storage and transport.
Tamper evidence - The narrow neck and one-time seal makes glass ampoules essentially tamper-proof. Any breach of the ampoule is immediately obvious.
Shatter resistance - Although glass can theoretically shatter, modern manufacturing standards require ampoules to be extremely durable and able to withstand pressure, shock, and reasonable flexing without breaking.
Hermetic seal - When sealed correctly with an oxygen flame, glass ampoules are impermeable to gasses and water vapor. They offer reliable containment without leakage.
Optical clarity - Clear glass allows easy visual inspection of the quality and fill level of the solution. Certain glass colors also protect solutions sensitive to visible or UV light.
Glass Ampoule Manufacturing Process
Producing consistent, high quality ampoules requires expertise in glassblowing as well as quality control at each stage:
- Glass tubing selection - Choosing tubing with consistent wall thickness and few imperfections ensures the ampoules will have uniform strength and sealing ability.
- Annealing - Heating followed by slow cooling removes internal stresses developed during the tubing's original glass molding process. This prevents weaknesses that could lead cracks or breaks.
- Cutting tubing - A diamond saw blade or ceramic wheel precisely cuts the glass into segments of specified length without cracks or debris.
- Molding ampoules - Through a combination of heat and physical manipulation by skilled workers, one end of the glass segments is melted and shaped into the desired ampoule form. An intermediate stress relief annealing cycle may be included depending on the glass thickness.
- Filling and sealing - Once cooled, the open ampoules are filled with a precise amount pharmaceutical solution by weight or volume. The second end is then melted shut to seal the contents inside.
- Final annealing - A final, overnight annealing with slow cooling ensures all new stresses from molding and sealing are relieved for a strong final product.
- Washing - Sterile purified water washes remove debris, cold end seals, lubricants, carbon deposits, and other contaminants.
- Drying & packing - Ampoules are dried, inspected one by one, and packed in containers designed to prevent breakage during transportation and storage.
Standards for Glass Ampoules
Medical glass ampoules must adhere to pharmaceutical packaging standards like USP or EP to meet regulatory compliance in most countries. These include specifications like:
- Hydrolytic resistance - passivation with sulfur dioxide and limits on alkali ions that could react with contents
- Quality control tests - sample testing for dimensions, thermal shock resistance, water permeability, mechanical stress resistance
- Restricted heavy metals - low levels of lead, arsenic, and other toxic elements
- Defect limits - standards for cracks, stones, bubbles, thin spots and other flaws
An established, certified glass ampoule manufacturer will have documented procedures following cGMP, ISO 9000, or similar quality guidelines. Their manufacturing facilities will also pass periodic inspections by pharmaceutical regulators.
Choosing a Reliable Glass Ampoule Manufacturer
Not all glass ampoule suppliers can produce medical-grade ampoules suitable for pharmaceutical use. Here are key factors to consider:
Quality Systems - Stringent quality control at every stage, following cGMP, ISO, EP or similar guidelines shows commitment to consistency.
Testing Capabilities - Dimensional gauging, hydrolytic testing, thermal/pressure/stress testing indicates an advanced QA/QC department.
Certifications - Compliance certifications like ISO 9001, validation by regulators like US FDA, CE marking, etc. verify standards adherence.
Experience - Look for decades, or better yet generations of glassworking expertise applied to pharmaceutical containers. New suppliers lack proof.
Packaging & Transport - Purpose-built containers and experienced logistics partners prevent damage in transit.
R&D Investment - State-of-the-art molding machinery and continuous improvement through testing shows dedication to progress.
Range of Products - Varied ampoule sizes and colors indicates flexibility - a good sign for custom projects.
Stability - Consistent top management and highly skilled workers creates stability and retention of manufacturing knowledge.
By selecting an established company focused on quality, regulatory compliance, and continuous improvement, pharmaceutical brands can be confident in consistent, reliable glass ampoules that safely contain their valuable drug products through the supply chain.
Advantages of Glass Ampoules for Pharmaceuticals
While plastic vials have grown in popularity, glass ampoules retain distinct advantages that continue to make them the gold standard for many applications.
Oxygen Sensitivity - Unlike inert glass, all plastics are at least slightly oxygen permeable. Oxygen can degrade many pharmaceutical molecules. Glass ampoules provide a true hermetic barrier.
Sterilization - Glass ampoules can be autoclaved for assured sterility. Most plastics do not withstand autoclaving temperatures and must rely on chemical surface sterilants with less certainty.
Long Term Stability - Glass transparency makes inspection simple through distribution chains. Plastic polymers can interact with drug products and unpredictable ways long term. Glass provides lifelong inertness.
Higher Concentrations - For highly concentrated drugs that interact with plastic polymers, non-reactive glass allows formulating solutions not possible in plastic containers.
Security - Narrow necks, positive seals, and glass fragility provide clear, irreversible indications of tampering unavailable with plastic vials. This deters misuse.
Despite occasional breakability concerns, glass ampoules continue providing the highest level of security, stability, and compatibility for pharmaceutical solutions with significant advantages over plastic.
Types of Drugs Packaged in Glass Ampoules
While any injectable drug is theoretically compatible with glass ampoules, they remain the standard delivery method for certain classes of pharmaceuticals.
Vaccines - As the backbone of public health disease prevention for over a century, vaccines benefit greatly enhanced stability from inert glass storage over decades.
Antibiotics - From penicillin onwards, adversarial bacteria demand high concentration antibiotics like carbapenems be maintained at full potency by impermeable glass.
Biologics & Biotech Injectables - The latest wave of antibody, protein, and nucleic acid therapies require absolute prevention of contamination during administration - uniquely offered by glass ampoules positive-displacement design.
Cytotoxic Chemotherapy - Highly aggressive anticancer drugs would interact adversely with plastic polymers making inert glass the only choice for safe containment.
Ophthalmics - Precise single-use sterile doses of ophthalmic irrigating solutions, cycloplegics and mydriatics must retain purity enabled by glass ampoule design.
While plastic packaging dominates consumer healthcare, glass ampoules provide vital capabilities allowing cutting-edge drugs to safely support health into the future.
The Future of Glass Ampoules
Despite over a century of proven performance, glass ampoules continue evolving to meet pharmaceutical demands. Recent innovations include:
- Color coded ampoules - tinted glass types indicating drug type, concentration, or usage guidelines.
- Translucent colored bars - allowing easy visual orientation of ampoule when filled with clear solutions.
- Tubular glass inserts - secondary internal tube providing breakage protection or separation of multiple drug components.
- Quick cooling processes - new heat transfer tech shortens production time for high volume lines.
- Robotic assist machinery - automating dangerous steps for improved worker comfort and safety.
By merging tradition with innovation, glass ampoules will keep supporting life-saving drugs through coming decades. Choose an experienced partner providing cutting-edge products.
Nantong Xinde Medical Packing Material Co., Ltd.
As a specialized manufacturer of pharmaceutical containers for over 15 years, Nantong Xinde Medical Packing Material Co. produces top quality glass ampoules supporting health standards worldwide. Their comprehensive production systems and stringent quality management serves international clients in meeting regulatory requirements across global markets.
State of the art machinery manned by highly experienced glassworkers enables flexibility in producing custom ampoule dimensions and colors at scale matching client needs. Ranging from tiny ampoules for ophthalmics to large volume IV solutions, formats can be tailored for specific drug profiles.
Closely following ISO 9001 guidelines and passing regular inspections by Chinese and international authorities, they provide fully documented manufacturing records for complete quality assurance. Facilities allow handling potent cytotoxic chemotherapy drugs safely during filling when required by clients.
Offering additional plastic packaging capabilities beyond leading glass ampoule production allows Nantong Xinde Medical to serve as astrategic one-stop partner for end-to-end pharmaceutical packaging needs.
With stability founded on sincerity, transparency and good faith, Nantong Xinde Medical Packing Material Co. delivers exceptional products on schedule to help bring pharmaceutical brands success across international markets. Contact them today to experience their dedication and quality firsthand!
Previous page
Previous page
More News

Customer message